Engineers at UEC-Aviadvigatel integrated modern materials and sophisticated technologies into the PD-14 production aircraft engine.
The PD-14’s design incorporates aerodynamic carbon fiber grids. They guarantee the engine’s reverse system’s dependable operation, regardless of the possibility of individual component damage.
Innovative Russian technology enables the creation of a monolithic cellular structure that is equally durable.
The Central Research Institute of Special Machinery is noteworthy for its production of the aerodynamic carbon fiber grids for the PD-14 aircraft engines.
An aircraft engine reverse system, also referred to as a thrust reverser, is a device that redirects the engine’s propulsion forward to assist in the aircraft’s descent after landing. This system is essential for improving safety while decreasing landing distances.
There are several types of thrust reversers. Turbofan engines frequently use the cascade type, which reroutes the exhaust flow using a sequence of movable vanes. Turbojet engines often use clamshell doors, which open to redirect and obstruct the exhaust flow. Military aircraft frequently employ the bucket type, which is characterized by pivoting containers that redirect thrust forward.
During landing, the pilot activates thrust reversers by deploying them, typically by drawing on the thrust levers or using a dedicated switch. Upon activation, the system redirects the engine’s exhaust flow forward, producing a decelerating impulse perpendicular to the aircraft’s flight path. This redirection allows the aircraft to decelerate more swiftly, resulting in shorter stopping distances on runways.
Thrust reversers offer substantial advantages. They significantly reduce the landing distance necessary for an aircraft, which is particularly advantageous on shorter runways. Furthermore, they offer an additional braking capability that is notably beneficial in emergencies or adverse weather conditions, thereby enhancing safety.
It is important to recognize that aircraft typically use thrust reversers only during landings and sporadically during go-arounds, which occur when an aircraft aborts a landing. Careful design is necessary to prevent damage during use and ensure they do not disrupt standard flight operations.
Unlike most aviation gas turbine engines, which use reverse systems with conventional hydraulic drives, the PD-14 has an electric drive. This breakthrough represents the very first use of this technology in a Russian power plant. This electric propulsion system offers many advantages. Initially, it reduces the product’s overall weight. Secondly, electric propulsion is more dependable and has a longer service life than conventional hydraulic systems. Third, the absence of toxic fluids typically associated with hydraulic systems improves the engine’s environmental performance. Fourth, a significant reduction in the engine’s fire hazard enhances operational safety.
Furthermore, this technology enables pilots to exert more flexible control over the movement of the equipment, improving their handling capabilities.
For context, an electric drive weighs only 57 kg, while a conventional hydraulic drive weighs approximately 80 kg. Electric drives can reduce an aircraft’s weight by more than 40 kg, enhancing its overall efficiency and performance, especially considering that an aircraft typically has two engines.
The Technodinamika holding company, which is a subsidiary of Rostec, has developed the electric reverse drive movement system. According to Maxim Kuzyuk, the CEO of Technodinamika, the development of electric reverser motors for the MC-21 represents a significant advancement towards the concept of a “more electric aircraft.”
As per Kuzyuk, “This concept is being actively developed all over the world since the rejection of hydraulic and pneumatic systems significantly reduces the weight and increases the reliability of the aircraft, and we have the opportunity to implement this solution in the most modern Russian engine. This will give us significant market advantages as an integrator of systems.”
The PD-14 is a turbojet twin-circuit twin-shaft engine (TRDD) that features a direct (gearless) fan drive and discrete flow outflow from the outer and inner circuits. The main developer is the Perm-based company “Aviadvigatel.” In takeoff mode, the PD-14 generates a thrust of 14,000 kgf and weights 2,870 kg. The engine can extend the flight range to 5,100 km, with the potential to enhance it to 7,000 km in the future.
According to the developers, its specific fuel consumption (kg/kgf·h) during cruise mode is 10–15% lower than that of comparable engines from other manufacturers.
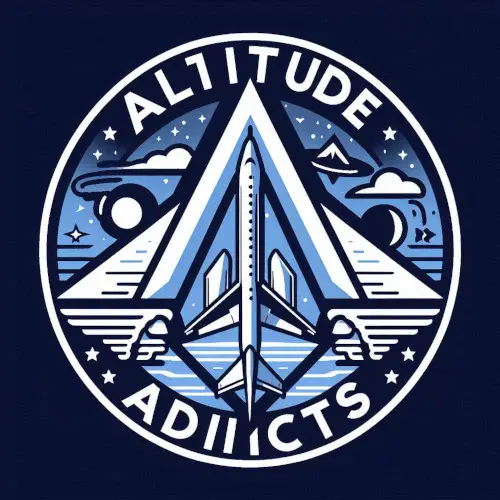
Official Website of Youtube Channel – Altitude Addicts