A recent video by blogger Maksim Gorshenin highlighted using the K1986VE92FI microcontroller, developed by the Russian company Milandr, in the PD-14 aircraft engines that power the MC-21 civilian aircraft. This information was shared during an interview with Yuriy Denisov, head of the robotics development department at “Aquarius,” on December 23, 2024.
PD-14 employs a complex network of embedded systems and microcontrollers distributed throughout the engine’s various subsystems.
The K1986VE92FI is a 32-bit microcontroller that operates at a clock frequency of up to 80 MHz. It features 128 KB of Flash memory and 32 KB of RAM. Notably, each PD-14 engine utilizes 12 of these microcontrollers, underscoring their critical role in aviation technology. Denisov emphasized that microcontrollers are fundamental to various industries, stating, “Not everything depends on processors; controllers form the backbone of the entire industry—cars, airplanes, ships.”
So what could be the advantages of this microcontroller? This is a speculation based on the role microcontrollers play in aviation technology.
The PD-14 engine’s efficiency is significantly improved by the microcontroller. It facilitates real-time data processing, which enables the PD-14 engine to monitor a variety of parameters, including fuel flow, pressure, and temperature. This capability guarantees optimal performance in a variety of operational environments, thereby enhancing engine reliability and fuel efficiency. The microcontroller is capable of supporting sophisticated control algorithms that can adjust to evolving flight conditions. Long-haul flights need to maintain optimal thrust and gasoline consumption by dynamically adjusting engine parameters.
The PD-14 engine operates at turbine inlet temperatures that are 60 to 80°C lower than those of its competitors. As a result of this decrease in temperature, engine components experience less degradation and their maintenance intervals are extended, resulting in a decrease in operating costs. By regulating combustion processes, the microcontroller facilitates the efficient management of these temperature levels.
The PD-14 engine’s modular design facilitates faster servicing and simpler maintenance. The microcontroller enables the identification and prompt resolution of any issues without necessitating extensive outages by enabling the diagnostics and monitoring of individual modules.
The microcontroller enhances the efficiency of fuel injection and combustion processes, resulting in a specific fuel consumption rate of 0.526 kg/kgf×hr (kilograms of fuel consumed for each kilogram-force of thrust produced by the engine in one hour). This efficacy is essential for airlines that are seeking to optimize payload capacity and range while reducing operational costs. The microcontroller assists the PD-14 engine in adhering to rigorous emissions regulations by facilitating precise control over combustion parameters. This is becoming increasingly significant in a market that places a high value on environmental sustainability in addition to performance.
The K1986VE92FI microcontroller is the primary component of the PD-14 engine; however, it is likely to be supplemented by other microcontrollers to oversee the engine’s numerous systems. The PD-14 lacks comprehensive documentation regarding the specific details of the additional microcontrollers that are employed.
The company “UEC-STAR” developed the two-channel automatic control system, SAU-14, for the PD-14 engine. This system ensures the engine’s reliability and efficiency by regulating its operational modes. This control system has a microprocessor that executes numerous critical functions. Initially, it monitors engine health by monitoring performance parameters in real-time, such as temperature, pressure, and speed. Secondly, it optimizes operation by adjusting engine parameters by the collected data to reduce fuel consumption and achieve maximum efficiency. Finally, the control system improves safety by automatically terminating the engine or altering its operating mode in the event of an abnormal circumstance. This sophisticated integration of technology not only enhances performance but also contributes to the overall safety and reliability of contemporary aviation systems.
The PD-14 engine, developed by Aviadvigatel, represents a significant advancement in Russian aviation technology. It was designed specifically for the MC-21 aircraft and incorporates several modern technologies to compete with Western engines like the Pratt & Whitney PW1400G. The PD-14 is characterized by features such as wide-chord titanium blades and advanced combustion chamber designs, aimed at improving fuel efficiency and reducing emissions.
The development of the PD-14 engine began in the early 2000s as part of Russia’s efforts to regain competitiveness in global aviation markets following decades of reliance on outdated technology. The engine received certification from Russian authorities in 2018 and is seen as a crucial step towards achieving self-sufficiency in aircraft engine production.
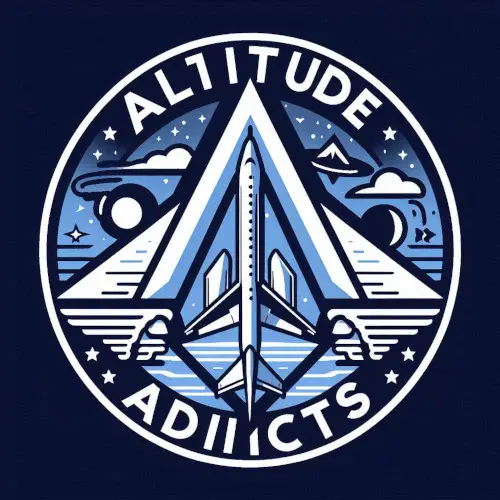
Official Website of Youtube Channel – Altitude Addicts